Wool From Fleece To Fabric
Wool Processing
Witness the incredible journey of wool! Starting as a raw fleece containing natural oils and debris, it’s shorn from the sheep and carefully skirted and sorted by quality. Impurities are washed away during scouring, and the tangled fibers are opened and aligned through carding, forming a sliver. For a refined touch, combing creates a smoother sliver for worsted yarns. The sliver is then elongated (drawing) and given strength through spinning into yarn. This yarn is then structured into fabric by weaving or knitting, and a range of finishing techniques perfect its final form and properties.:
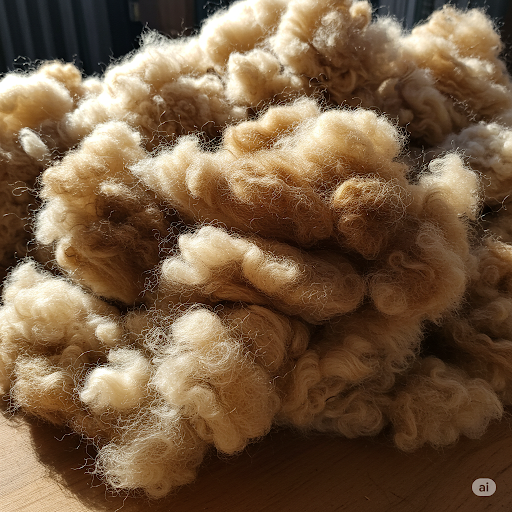
- Shearing: The process begins with removing the wool fleece from the sheep, usually done once a year. The shorn fleece is called “grease wool” because it contains natural oils (lanolin), sweat, dirt, and other impurities.
- Skirting and Sorting: The raw fleece is laid out on a table, and the lower-quality parts (e.g., from the legs and rear) are removed – this is called skirting. The remaining fleece is then sorted by hand based on fiber fineness, length (staple length), crimp (the natural waviness of the fiber), color, and any remaining impurities. Different grades of wool are suitable for different end uses.
- Scouring (Washing): The sorted wool is then cleaned to remove the grease, dirt, and other organic matter. This is typically done by washing the wool in a series of warm, soapy water baths. Sometimes, an acid bath (carbonizing) is used to remove any remaining vegetable matter. The goal is to get clean wool without damaging the fibers or causing excessive tangling (felting).
- Carding: Once the wool is clean and dried, it goes through a process called carding. This involves passing the wool fibers through a series of rollers covered with fine teeth or wires. Carding disentangles the wool fibers, aligns them in a somewhat parallel fashion, and removes any remaining short or broken fibers and impurities. The result is a continuous, untwisted strand of fibers called a sliver or roving. For a softer, more insulating yarn (woolen), the fibers are left in a more random arrangement after carding.
- Combing (Optional): For the production of worsted yarns, which are used for smoother, finer fabrics, an additional step called combing is performed after carding. Combing further aligns the longer fibers and removes the shorter ones (noils), resulting in a smoother, stronger sliver.
- Drawing: The sliver is then drawn out, a process of stretching and thinning it to a more consistent diameter. This may be done in several stages to achieve the desired fineness for spinning.
- Spinning: In this crucial step, the drawn-out fibers are twisted together to create a continuous yarn. The twist provides strength and holds the fibers together. Spinning can be done using various methods and machinery, from traditional spinning wheels to modern industrial spinning frames. The amount of twist influences the yarn’s characteristics – more twist creates a stronger, less soft yarn.
- Winding: The spun yarn is wound onto bobbins or cones, preparing it for the next stage of fabric production.
- Weaving or Knitting: The yarn is then used to create fabric through either weaving or knitting.
- Weaving: Involves interlacing two sets of yarns at right angles – the warp (lengthwise yarns) and the weft (crosswise yarns) – on a loom.
- Knitting: Consists of creating interlocking loops of yarn using needles.
- Finishing: The final fabric undergoes various finishing processes to improve its appearance, texture, and performance. These can include:
- Fulling: A process involving moisture, heat, and mechanical action that causes the wool fibers to shrink and interlock, resulting in a denser, more compact fabric (especially for woolen fabrics).
- Scouring (again): To remove any remaining processing oils or impurities.
- Dyeing: Adding color to the fabric. This can be done at various stages, from the raw wool to the finished fabric.
- Raising (Napping): Brushing the fabric surface to create a soft, fuzzy texture (e.g., flannel).
- Shearing: Leveling the raised surface for a uniform finish.
- Pressing: Smoothing out wrinkles and setting the fabric.
- Other treatments: To add properties like water resistance, mothproofing, or shrink resistance.