Resin Application on Denim Jeans: Creating Lasting Effects
Resin application on denim jeans is a finishing technique used to impart specific characteristics to the fabric, most notably stiffness, wrinkle resistance (or the setting of intentional wrinkles), and sometimes a slight sheen. It’s a process that involves chemical treatment followed by heat curing in an oven. Here’s a detailed lecture on the process:
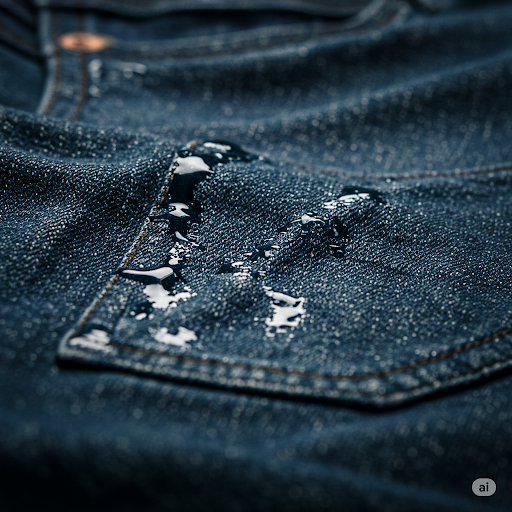
I. Purpose and Effects of Resin Application:
- Stiffness: Resin creates a film on the fabric surface and within the fibers, leading to a stiffer hand feel. The degree of stiffness can be controlled by the type and amount of resin used.
- Wrinkle Resistance/Setting: Resins cross-link the cellulose fibers in the cotton, making them more resistant to wrinkling. Conversely, if the jeans are manipulated (e.g., twisted, creased) before resin application and curing, the wrinkles can be permanently set in place, creating a crinkled or vintage look.
- Dimensional Stability: Resin treatment can help reduce shrinkage in denim.
- Enhanced Appearance: Some resins can impart a slight sheen or change the texture of the denim surface.
- Preparation for Other Finishes: Resin treatment can sometimes be a base for other finishing techniques like sandblasting, as it can make the abraded areas stand out more.
II. Chemicals Used in Resin Application:
The primary chemicals involved are synthetic resins. Several types are used in denim finishing, each offering slightly different properties:
- Urea-Formaldehyde (UF) Resins: These were among the earliest and are still used due to their effectiveness and relatively low cost. However, they can release formaldehyde, which is a health concern, so low-formaldehyde or formaldehyde-free options are increasingly preferred.
- Glyoxal-Based Resins: These are a common low-formaldehyde alternative offering good wrinkle resistance and stiffness.
- Acryl Resins: These can provide a range of finishes from soft to stiff and offer good durability.
- Polyurethane Resins: These offer flexibility and can be used for specific effects like coating or creating a leather-like feel.
- Ketone Resins: Another type of cross-linking resin with varying properties.
- Silicone Softeners (Often added to the resin bath): To counteract the harshness that some resins can impart and improve the hand feel.
- Wetting Agents: To ensure even penetration of the resin into the denim fabric.
- Catalysts: To initiate and speed up the cross-linking reaction during the oven curing stage. These are often salts of acids like magnesium chloride.
- pH Adjusters (e.g., Acetic Acid): To maintain the optimal pH for the resin application and curing process.
III. Recipe and Method of Application:
The specific recipe will vary depending on the desired effect, the type of denim, and the resin being used. However, a general outline of the process includes:
- Garment Preparation: The denim jeans are typically cut and sewn into their final shape before resin application. They might undergo pre-washing or other treatments depending on the desired final look.
- Resin Bath Preparation: A solution containing the chosen resin, catalyst, wetting agent, and often a softener, is prepared in a large tank. The concentration of the resin will determine the stiffness and the level of wrinkle resistance/setting. Typical resin concentrations can range from 5% to 20% of the bath volume.
- Application Methods:
- Garment Dip: The most common method involves fully immersing the jeans in the resin bath, ensuring thorough saturation of the fabric.
- Spraying: For more targeted application or to create specific effects (like setting intentional wrinkles), the resin solution can be sprayed onto the garments as they tumble in a rotating drum or while placed on mannequins.
- Padding: The fabric can be passed through rollers that are saturated with the resin solution, ensuring even application. This is more common for fabric finishing before garment construction but can be used for specific effects on finished garments.
- Excess Removal (Extraction): After dipping or spraying, excess resin solution is typically removed using a hydro-extractor, reducing the wet pick-up to a controlled level (e.g., around 60-70% weight of the fabric).
- Wrinkle Formation (if desired): If a crinkled or vintage look with set wrinkles is the goal, the jeans are manually or mechanically manipulated (twisted, creased, tied with threads, clipped) at this stage to create the desired wrinkle patterns.
- Oven Treatment (Curing): This is a critical step where the resin undergoes a chemical reaction (cross-linking) under heat, permanently fixing the resin within and on the fabric fibers and setting any intentional wrinkles. The jeans are placed in a large industrial oven, and the curing temperature typically ranges from 120°C to 170°C (250°F to 340°F) for a duration of 5 to 20 minutes, depending on the resin type and the desired level of curing. Insufficient curing can lead to formaldehyde release and poor performance of the resin finish.
- Post-Curing Treatments (Optional): After curing, the jeans may undergo further processing, such as:
- Washing: To remove any unreacted resin or chemicals.
- Softening: Additional softening agents might be applied to improve the hand feel if the resin has made the fabric too stiff.
- Other Finishing Techniques: Sandblasting, stone washing, or other distressing methods can be applied after resin treatment to enhance specific areas or create a layered effect.
IV. Factors Affecting the Resin Treatment:
- Type of Resin: Different resins offer varying degrees of stiffness, wrinkle resistance, and hand feel.
- Concentration of Resin Bath: Higher concentrations lead to stiffer fabrics and better wrinkle resistance/setting.
- Catalyst Type and Concentration: Affects the rate and degree of cross-linking during curing.
- Temperature and Duration of Oven Treatment: Crucial for proper curing and achieving the desired finish.
- Wet Pick-up: The amount of resin solution absorbed by the fabric affects the final result.
- Type and Construction of Denim: The weight, weave, and fiber content of the denim will influence how the resin interacts with the fabric.
V. Safety and Environmental Considerations:
- Formaldehyde Emission: The use of formaldehyde-based resins requires careful monitoring and control of the curing process to minimize formaldehyde release, which is a health hazard. Low-formaldehyde and formaldehyde-free resins are preferred.
- Chemical Handling and Disposal: Proper handling, storage, and disposal of all chemicals used in the resin treatment process are essential to protect workers and the environment.
- Ventilation: Adequate ventilation is required in the application and curing areas to prevent the inhalation of chemical vapors.
- Personal Protective Equipment (PPE): Workers must wear appropriate PPE, including gloves, masks, and eye protection.
VI. Conclusion:
Resin application is a versatile finishing technique that allows denim manufacturers to impart specific performance and aesthetic characteristics to jeans. By carefully selecting the appropriate chemicals, controlling the application method, and precisely managing the oven treatment, it’s possible to create everything from wrinkle-resistant workwear to fashion-forward jeans with permanently set creases and a unique hand feel. Understanding the intricacies of this process, along with its safety and environmental considerations, is crucial for responsible and effective denim production.