Regenerated Cellulosic Fiber: Viscose Rayon – A Detailed Lecture (#5 in a Series on Cellulosic Fibers)
Good morning, everyone. Welcome back to our series on cellulosic fibers. Today, we’re focusing on a crucial category: regenerated cellulosic fibers, and we’ll be taking a deep dive into one of its most historically significant and widely utilized members: Viscose Rayon.
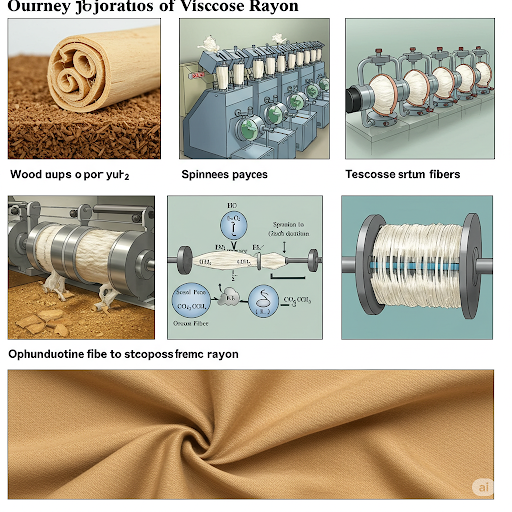
As we’ve discussed previously, natural cellulosic fibers like cotton, linen, and hemp are derived directly from plant sources. Regenerated cellulosic fibers, on the other hand, are created by chemically processing natural cellulose materials, typically wood pulp or cotton linters, to form a viscous solution which is then spun into fibers. Viscose rayon was the first manufactured fiber and revolutionized the textile industry, offering a more affordable alternative to silk and possessing unique properties that made it highly desirable.
The Production Process of Viscose Rayon:
The production of viscose rayon is a multi-step chemical process:
- Source Material: The primary source of cellulose for viscose production is purified wood pulp, often derived from fast-growing trees like eucalyptus, pine, or beech. Cotton linters, the short fibers remaining on cotton seeds after ginning, can also be used. The chosen cellulose source is processed to obtain a high-purity cellulose pulp.
- Alkalization: The cellulose pulp is treated with a strong alkali solution, typically sodium hydroxide (NaOH). This process causes the cellulose to swell and form alkali cellulose. The reaction can be represented as:
Cellulose - OH + NaOH → Cellulose - ONa + H₂O
The alkali cellulose is then shredded into crumbs to increase its surface area for the next reaction. - Xanthation: The alkali cellulose crumbs are reacted with carbon disulfide (CS₂) in a process called xanthation. This chemical reaction forms sodium cellulose xanthate, a soluble cellulose derivative. The xanthate is an orange-colored compound and is soluble in dilute alkali. The reaction can be represented as:
Cellulose - ONa + CS₂ → Cellulose - O - CSSNa
The resulting solution is viscous and honey-like, hence the name “viscose.” - Dissolving: The sodium cellulose xanthate is dissolved in a dilute solution of sodium hydroxide (NaOH). This creates the viscose solution, which is then filtered to remove any undissolved particles. The viscose solution is typically aged for a specific period to achieve the desired viscosity and maturity for spinning.
- Spinning (Wet Spinning): The mature viscose solution is forced through spinnerets, which are small nozzles with numerous tiny holes. The spinnerets are submerged in a spin bath containing sulfuric acid (H₂SO₄), sodium sulfate (Na₂SO₄), and zinc sulfate (ZnSO₄). As the viscose stream enters the acidic spin bath, the sodium cellulose xanthate is regenerated back into cellulose in the form of continuous filaments. The acid neutralizes the sodium xanthate and decomposes it, releasing carbon disulfide and forming cellulose. The chemical reaction is complex but can be broadly represented as a reversal of the xanthation and alkalization steps.
- Drawing and Stretching: As the filaments emerge from the spinneret, they are drawn or stretched. This process aligns the cellulose molecules within the fibers, increasing their strength and reducing their denier (fineness).
- Washing: The newly formed rayon filaments are thoroughly washed to remove residual chemicals from the spin bath, such as sulfuric acid and salts.
- Cutting (if staple fiber): If the desired end product is staple fiber (short fibers used for spinning into yarns), the continuous filaments are cut to specific lengths, similar to natural fibers like cotton or wool. If continuous filaments are desired (for example, for some types of fabrics or industrial uses), this step is skipped.
- Bleaching (optional): If a whiter fiber is required, the rayon can be bleached using hydrogen peroxide or other bleaching agents.
- Drying: Finally, the rayon fibers are dried to remove moisture. This can be done using various methods, such as air drying or mechanical drying.
Characteristics of Viscose Rayon Fiber:
Viscose rayon possesses a unique set of properties that contribute to its wide range of applications:
- Structure: Viscose rayon fibers are relatively uniform in cross-section and have a characteristic serrated or irregular surface, which contributes to its luster and dyeability.
- Chemical Composition: It is almost pure cellulose, similar to natural cellulosic fibers, but the arrangement of the cellulose molecules is less crystalline.
- Length: Viscose rayon can be produced in both filament (continuous) and staple (short, cut) forms, allowing it to mimic the characteristics of silk or cotton/wool, respectively.
- Fineness: The fineness of viscose rayon fibers can be controlled during the manufacturing process to produce fibers of varying deniers.
- Strength (Tenacity): Viscose rayon has moderate strength when dry (around 1.5-2.4 gm/denier), but its strength significantly decreases (by about 50%) when wet. This is a key limitation of standard viscose rayon.
- Elasticity: Viscose rayon has low elasticity and resilience, meaning it wrinkles easily and does not readily return to its original shape after stretching.
- Absorbency: Viscose rayon is highly absorbent, even more so than cotton. This is due to the amorphous regions in its cellulose structure, which allow water molecules to penetrate easily. This high absorbency makes it comfortable for clothing and suitable for applications like towels.
- Breathability: The absorbent nature and porous structure of viscose rayon contribute to good breathability, allowing air and moisture to pass through the fabric.
- Thermal Properties: Viscose rayon is a poor conductor of heat, providing some insulation. It is not thermoplastic and will burn readily.
- Luster: Viscose rayon has a high luster, which can be controlled during manufacturing to range from a bright sheen to a more subdued appearance. This silklike luster was one of its primary appeals initially.
- Affinity for Dyes: Viscose rayon has excellent affinity for a wide range of dyes, resulting in vibrant and colorfast fabrics.
- Resistance to Static Electricity: Due to its good moisture absorption, viscose rayon does not tend to build up static electricity.
- Effect of Chemicals: Viscose rayon is sensitive to strong acids, which can cause it to degrade. It is more resistant to alkalis than acids but can be damaged by strong, prolonged exposure.
- Biodegradability: Being cellulose-based, viscose rayon is biodegradable under appropriate conditions.
- Comfort: The softness and high absorbency of viscose rayon make it comfortable to wear, especially in warm weather.
- Drape: Viscose rayon fabrics typically have excellent drape, meaning they hang well and flow gracefully.
End Uses of Viscose Rayon Fiber:
The versatile properties of viscose rayon have led to its widespread use in numerous applications:
- Apparel: Viscose rayon is used extensively in clothing, including blouses, dresses, skirts, lingerie, linings, suits, and knitwear. Its soft drape and comfort make it a popular choice.
- Home Textiles: It is used in bedding (sheets, blankets), towels (for its absorbency), curtains, and upholstery.
- Industrial Applications: Rayon is used in the production of tire cords (though less common now due to the advent of stronger synthetics), non-woven fabrics, and surgical dressings (due to its absorbency and biodegradability).
- Hygiene Products: Rayon’s high absorbency makes it suitable for use in products like sanitary napkins and disposable wipes.
- Blends: Viscose rayon is often blended with other fibers, both natural (like cotton) and synthetic (like polyester), to combine desirable properties and improve the performance and aesthetics of fabrics. For example, blending with polyester can improve wrinkle resistance and strength.
Environmental Considerations of Viscose Rayon Production:
While viscose rayon is derived from a renewable resource (cellulose), its production process has historically been associated with significant environmental concerns:
- Use of Hazardous Chemicals: The process involves the use of carbon disulfide (CS₂), a toxic chemical that poses risks to both workers and the environment.
- Water Pollution: Wastewater from the viscose process can contain various pollutants, including heavy metals and sulfur compounds, if not properly treated.
- Deforestation: The demand for wood pulp can contribute to deforestation if sustainable forestry practices are not followed.
However, there have been advancements in cleaner production technologies for viscose rayon, focusing on closed-loop systems that recycle chemicals and reduce emissions. Newer generations of regenerated cellulose fibers, like Lyocell (Tencel), have been developed with more environmentally friendly production processes.
Conclusion:
Viscose rayon, the first manufactured fiber, holds a significant place in the history of textiles. Its silklike luster, soft drape, and high absorbency made it a revolutionary material. While its production has faced environmental challenges, ongoing innovations are striving for more sustainable methods. Understanding the production, characteristics, and diverse applications of viscose rayon is crucial for anyone involved in the textile industry or interested in the evolution of materials.