Manufactured Fibers: An Introduction – Lecture (#12 in a Series on Textile Fibers)
Good morning, everyone. Today, we embark on a new section of our textile fiber journey, moving beyond the realm of natural fibers and into the world of manufactured fibers. These are fibers that are created or synthesized by humans, often from raw materials that are not inherently fibrous. Understanding manufactured fibers is crucial in today’s textile industry, as they constitute a significant portion of the materials we use for clothing, home furnishings, and industrial applications.
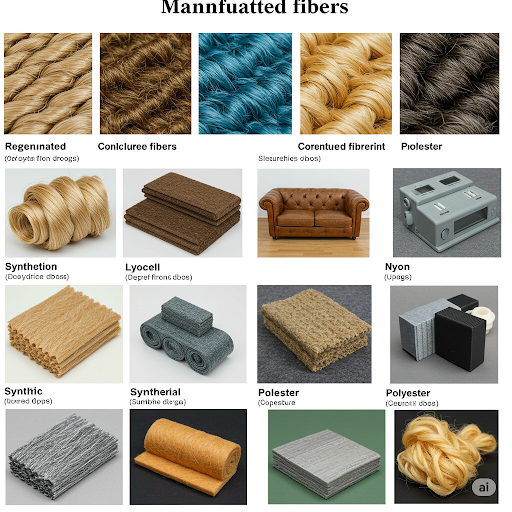
What are Manufactured Fibers?
Manufactured fibers are defined as fibers that are produced from chemical compounds or by modifying natural substances. Unlike natural fibers, which are directly obtained from plants or animals, manufactured fibers are engineered to possess specific properties and characteristics tailored for particular end uses. This ability to manipulate the fiber’s structure and composition at a molecular level gives manufactured fibers a vast range of possibilities in terms of strength, elasticity, texture, and other performance attributes.
Two Main Categories of Manufactured Fibers:
Manufactured fibers are broadly classified into two main categories based on their origin and production:
- Regenerated Fibers: These fibers are produced from naturally occurring polymers (long chains of repeating molecular units) that have been chemically processed and regenerated into fiber form. The source polymers are typically cellulose (from wood pulp or cotton linters) or protein (from soybeans or milk). We have already explored some key regenerated cellulosic fibers like viscose rayon and acetate rayon.
- Synthetic Fibers: These fibers are synthesized from chemical compounds, often derived from petroleum byproducts. These raw materials are polymerized (joined together into long chains) through chemical reactions to create the fiber-forming substances. Synthetic fibers are a product of modern chemistry and have revolutionized the textile industry with their unique properties.
Overview of Regenerated Fibers (Brief Recap and Introduction to Others):
As mentioned, we have already covered some important regenerated cellulosic fibers. To recap and introduce others:
- Regenerated Cellulosic Fibers:
- Viscose Rayon: Produced from cellulose xanthate solution. Known for its soft hand, good drape, and absorbency.
- Acetate Rayon: Produced from cellulose acetate. Known for its luster, drape, and lower absorbency.
- Lyocell (e.g., Tencel): Produced using a more environmentally friendly solvent spinning process from cellulose. Known for its strength, absorbency, and soft hand.
- Cupro (Cuprammonium Rayon): Produced by dissolving cellulose in a copper-ammonia solution. Known for its fine denier, soft hand, and good drape.
- Bamboo Rayon: Rayon produced using bamboo pulp as the cellulose source (often using the viscose process).
- Regenerated Protein Fibers: These are less common in the mainstream textile industry but are areas of ongoing research and development:
- Soybean Fiber (Soy Silk): Produced from the protein in soybean meal. Known for its soft hand, good drape, and moisture absorbency.
- Milk Protein Fiber (Casein Fiber): Produced from casein, the protein in milk. Known for its soft hand and potential for skin-friendly properties.
Introduction to Synthetic Fibers:
Synthetic fibers are a diverse group, each engineered with specific properties. The most common synthetic fibers include:
- Nylon (Polyamide): The first truly synthetic fiber, known for its high strength, elasticity, abrasion resistance, and ease of care.
- Polyester (Polyethylene Terephthalate – PET): The most widely used synthetic fiber globally, known for its strength, durability, wrinkle resistance, and hydrophobic nature.
- Acrylic: A synthetic fiber made from acrylonitrile, known for its wool-like bulk, softness, and warmth.
- Olefin (Polypropylene and Polyethylene): Lightweight, strong, hydrophobic fibers with good chemical resistance, used in carpets, upholstery, and technical applications.
- Spandex (Elastane): Highly elastic fiber known for its ability to stretch and recover, used in stretch fabrics and apparel.
- Specialty Synthetic Fibers: This category includes fibers with unique properties like high strength (e.g., aramids like Kevlar and Nomex), high performance (e.g., PTFE like Teflon), and other specialized characteristics.
General Advantages of Manufactured Fibers:
Manufactured fibers offer several advantages that have contributed to their widespread adoption:
- Tailored Properties: Fibers can be engineered with specific properties like strength, elasticity, absorbency, flame resistance, and wrinkle resistance to meet the demands of particular end uses.
- Consistency and Uniformity: Manufacturing processes allow for greater control over fiber diameter, length, and other physical characteristics, leading to more uniform yarns and fabrics.
- Abundance and Cost-Effectiveness (for some): Synthetic fibers, in particular, can often be produced in large quantities at relatively lower costs compared to some natural or specialty fibers.
- New Possibilities: Manufactured fibers have enabled the creation of textiles with properties not found in natural fibers, opening up new applications and performance levels.
General Disadvantages of Manufactured Fibers:
Manufactured fibers also have some drawbacks:
- Environmental Concerns: The production of some manufactured fibers, particularly synthetics derived from petroleum, can have significant environmental impacts related to resource depletion, energy consumption, and pollution.
- Lack of Natural Aesthetics and Hand (for some): While advancements are being made, some manufactured fibers may lack the unique textures, breathability, and natural aesthetic appeal of certain natural fibers.
- Static Electricity Buildup (for some synthetics): Hydrophobic synthetic fibers can tend to build up static electricity.
- Lower Absorbency (for some synthetics): Many synthetic fibers are hydrophobic (water-repelling), which can be a disadvantage in applications where moisture absorption is desired (e.g., clothing worn next to the skin).
Conclusion:
Manufactured fibers represent a vast and constantly evolving field within textile science. From the regeneration of natural polymers to the synthesis of entirely new materials, these fibers have dramatically expanded the possibilities of textile design and functionality. Understanding the fundamental categories of regenerated and synthetic fibers, along with their general advantages and disadvantages, provides a crucial foundation for exploring the specific characteristics and applications of individual manufactured fibers in our upcoming lectures.
In our next session, we will begin our detailed exploration of synthetic fibers, starting with one of the most versatile and widely used: nylon.