Coating on Denim Jeans and “Mirror Finish”: A Detailed Lecture
Good evening, everyone. Tonight, we’ll explore the world of coatings applied to denim jeans, a technique used for both functional and aesthetic purposes.
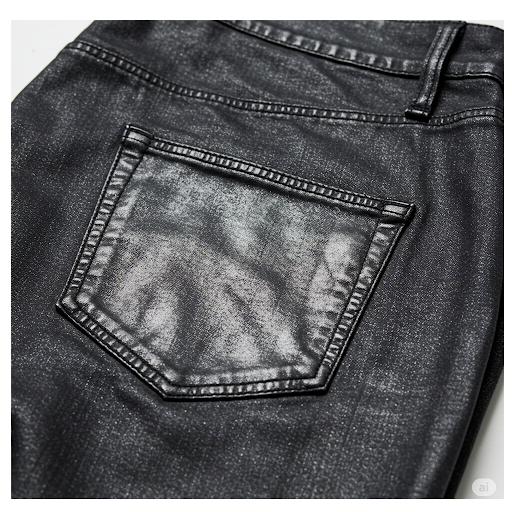
We will also revisit the ambitious concept of a “mirror finish” in this context, examining if coatings can contribute to such an effect, along with the chemicals, machinery, and methodologies involved.
I. Coating on Denim Jeans: Functionality and Aesthetics
Coating denim jeans involves applying a thin layer of a substance onto the fabric surface. This can achieve a variety of effects:
A. Functional Purposes:
- Water Resistance/Repellency: Certain coatings can make denim resistant to water, protecting the wearer from light rain or spills.
- Wind Resistance: A dense coating can reduce the permeability of air through the denim.
- Abrasion Resistance: Coatings can add a protective layer, increasing the durability of the jeans, especially in high-wear areas.
- Improved Hand Feel: Some coatings, particularly softer polymers, can alter the texture of the denim, making it smoother or more supple.
- Anti-Crease Properties: While resin treatments (discussed previously) are the primary method for wrinkle resistance, certain coatings can contribute to this.
B. Aesthetic Purposes:
- Luster and Shine: Coatings can impart varying degrees of sheen, from a subtle luster to a high gloss.
- Color Modification: Pigmented coatings can change the color of the denim or create unique surface effects.
- Textural Effects: Coatings can mimic the appearance of other materials like leather, wax, or rubber.
- Metallic Looks: Coatings containing metallic pigments can create silver, gold, or bronze finishes.
- Patterning: Coatings can be applied in specific patterns using techniques like screen printing or spraying.
II. Chemicals Used for Coating Denim:
A wide range of polymers and additives are used for coating denim, depending on the desired effect:
- Polyurethane (PU) Coatings: Versatile, offering good abrasion resistance, flexibility, and the potential for various finishes (matte, glossy, leather-like). Water-based PUs are increasingly preferred for environmental reasons.
- Acrylic Coatings: Can provide stiffness, durability, and are often used for pigmented coatings. They offer good wash fastness.
- Wax Coatings: Impart a water-resistant and often slightly stiff feel with a unique, sometimes crackled, appearance. Paraffin wax and synthetic waxes are used.
- Silicone Coatings: Primarily used for softening and water repellency, often providing a smooth, silky hand feel.
- Resin Coatings (Thermosetting Polymers): Similar to those used for wrinkle resistance, these can create a stiff finish and are durable after curing.
- Metallic Pigments and Binders: To achieve metallic effects, fine metallic powders (aluminum, copper, etc.) are mixed with a binder (often acrylic or polyurethane) and applied as a coating.
- Dyes and Pigments: For colored coatings, these are incorporated into the polymer matrix.
- Cross-linking Agents: To improve the durability and wash fastness of the coating.
- Adhesion Promoters: To ensure the coating adheres well to the denim fabric.
- Softening Agents: Added to counteract any harshness from the primary coating material.
- Water Repellents (e.g., Fluorocarbons): Incorporated for durable water repellency.
III. Machinery Used for Coating Denim:
Various machines are employed to apply coatings to denim garments or fabric:
- Padding Machines: Fabric is passed through a trough containing the coating solution and then through rollers that squeeze out excess liquid, ensuring even application. Primarily used for fabric coating before garment construction but can be adapted for some garment applications.
- Spray Coating Machines: The coating material is sprayed onto the garments as they move on a conveyor belt or tumble in a rotating drum. This allows for more targeted application and can create unique effects. Airbrushes or industrial spray guns are used.
- Roller Coating Machines: Similar to padding, but with more precise control over the amount of coating applied via engraved rollers.
- Knife Coating Machines: The coating is applied using a blade that spreads a controlled thickness of the material onto the fabric.
- Screen Printing Machines (Rotary or Flatbed): For applying patterned coatings or specific designs.
- Curing Ovens: After coating, garments often need to be passed through a curing oven at specific temperatures to dry the coating and initiate any cross-linking reactions, ensuring durability. The type of oven (convection, infrared) depends on the coating chemistry.
- Calenders: Heated rollers used to smooth the coating surface and enhance luster after application and curing.
IV. Methodology of Coating Denim:
The specific methodology depends heavily on the desired effect and the chosen coating material:
- Preparation: The denim garments are prepared (e.g., pre-washed).
- Coating Solution Preparation: The chosen polymer, pigments/dyes, additives, and any necessary solvents or water are mixed according to the recipe for the desired coating.
- Application: The coating solution is applied to the denim garments using one of the methods described above (padding, spraying, roller, knife, or screen printing). The number of layers and the amount of coating applied will influence the final effect.
- Drying: The coated garments are dried to remove any solvents or water from the coating. This is often done in tunnel dryers or static ovens at moderate temperatures.
- Curing (if necessary): For coatings that require cross-linking (e.g., some polyurethanes and resins), the garments are passed through a curing oven at a specific temperature and time to ensure the coating is durable and adheres well.
- Finishing (Optional): After curing, additional finishing steps like calendering (for increased luster) or softening treatments can be applied.
- Quality Control: The coated garments are inspected for evenness of application, desired aesthetic and functional properties, and durability.
V. The “Mirror Finish” Revisited with Coatings:
Achieving a true, highly reflective “mirror finish” on denim using coatings is still challenging and not a standard practice for typical denim jeans. However, coatings offer the most plausible route to get closer to this effect than modifying the raw denim itself.
Potential Coating Approaches for a “Mirror Finish”:
- High-Gloss Polyurethane or Acrylic Coatings: Applying multiple thin layers of a specifically formulated high-gloss PU or acrylic coating, followed by meticulous leveling and polishing (e.g., with a calender), might create a very shiny surface. However, the inherent texture of the denim would still likely diffuse the reflection to some extent.
- Metallic Coatings with a Smooth Top Layer: Applying a smooth, high-gloss clear coating over a metallic pigment coating could potentially yield a more reflective surface. The metallic particles would provide the reflectivity, and the smooth top layer would enhance the gloss.
- Lamination with a Reflective Film (as discussed previously): While not strictly a “coating” applied in liquid form, laminating a very thin, mirror-like film onto the denim surface would be the most direct way to achieve a reflective finish, albeit at the cost of the denim’s natural properties.
Challenges Specific to a Coating-Based “Mirror Finish”:
- Maintaining Reflectivity: The coating would need to be highly smooth and resistant to scratches and abrasion to maintain its mirror-like quality during wear and washing.
- Flexibility and Cracking: A thick, glossy coating might be prone to cracking at stress points.
- Adhesion: Ensuring the coating adheres strongly to the denim and doesn’t peel or flake off is crucial.
- Denim Texture: The underlying texture of the denim will always present a challenge to achieving a perfectly smooth, reflective surface.
VI. Conclusion:
Coating is a versatile technique that significantly expands the aesthetic and functional possibilities of denim jeans. While a true “mirror finish” in the literal sense remains an unconventional and challenging goal due to the inherent nature of denim, specialized high-gloss coatings, potentially combined with metallic pigments or lamination, offer the closest theoretical approaches. However, these methods would likely compromise the traditional feel, breathability, and durability associated with denim. The primary applications of coatings on denim remain focused on achieving specific fashion looks, enhancing performance, and adding unique textures, rather than creating a purely reflective surface.