The Amazing Stretch of Spandex: Textile Fiber Lecture #20 (in a Series on Textile Fibers)
Welcome back to our textile fiber lecture series! Today, we’re diving into the world of Spandex, a synthetic fiber renowned for its incredible elasticity and ability to stretch and recover repeatedly. This unique property has revolutionized the apparel industry, enabling the creation of comfortable and form-fitting garments for various activities. In this lecture, we will explore the history of spandex, its chemical composition, and the process of its creation.
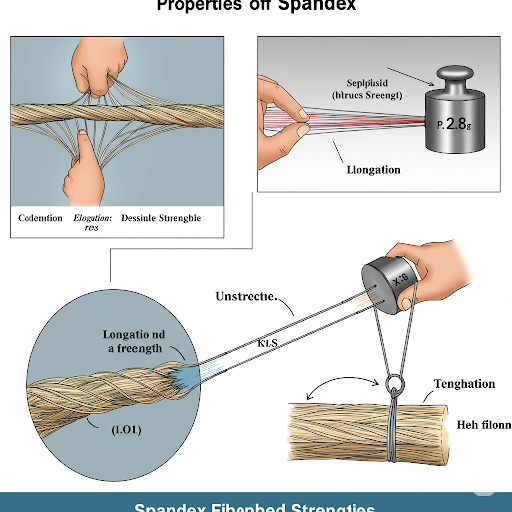
The Quest for a Better Elastic Fiber:
Before spandex, natural rubber was the primary elastic material used in textiles. However, rubber had limitations, including poor resistance to heat, oxidation, and chlorine. The search for a more durable and resilient elastic fiber led to the development of spandex.
Joseph Shivers, a chemist working at DuPont, is credited with the invention of spandex in 1958. DuPont commercially introduced the fiber under the brand name Lycra in 1959. Other manufacturers have since developed their own versions of spandex with different trade names.
The introduction of spandex had a profound impact on the apparel industry. It allowed for the creation of form-fitting sportswear, swimwear, hosiery, and intimate apparel that offered both comfort and freedom of movement. Its ability to recover its original shape after stretching made garments more durable and provided a better fit.
The Chemistry of Stretch: Composition and Preparation
Spandex is a synthetic fiber known for its exceptional elasticity (stretchability). It is classified as an elastomeric fiber, meaning it can be stretched to several times its original length and then return to its original size and shape. Spandex fibers are composed of a long-chain synthetic polymer called polyurethane, which is a block copolymer.
Composition and Preparation:
The production of spandex typically involves the reaction of a diisocyanate with a long-chain diol (polyether glycol or polyester glycol). The specific diisocyanate and glycol used can vary depending on the desired properties of the final fiber.
The general process involves the following steps:
- Polymerization: The diisocyanate and the glycol react to form a polyurethane prepolymer. This prepolymer contains reactive isocyanate (-NCO) end groups.
- Chain Extension: The prepolymer is then reacted with a chain extender, which is typically a low molecular weight diamine or diol. This chain extension reaction links the prepolymer molecules together, forming long, segmented polyurethane polymer chains. These chains consist of alternating soft segments (derived from the long-chain glycol, providing elasticity) and hard segments (derived from the diisocyanate and chain extender, providing strength and coherence).
- Spinning: The polyurethane polymer solution is then spun into fibers using one of three main spinning techniques:
- Dry Spinning: The polymer solution is extruded into a warm air chamber, where the solvent evaporates, leaving behind solid fibers.
- Wet Spinning: The polymer solution is extruded into a coagulation bath that causes the polymer to solidify.
- Reaction Spinning: The monomers react during the spinning process to form the polymer directly as fibers.
- Drawing and Heat Setting: The spun fibers are often drawn (stretched) to align the polymer molecules and improve their strength and elasticity. Heat setting is then applied to stabilize the stretched fibers and lock in their elastic properties.
Chemical Structure of Spandex (Polyurethane):
The chemical structure of spandex is complex due to the segmented nature of the polyurethane polymer. It consists of:
- Soft Segments: These are long, flexible polyether or polyester chains with low intermolecular forces, allowing for the stretching and recoiling of the fiber. Common glycols used include polyethylene glycol or polytetramethylene glycol.
- Hard Segments: These are shorter, more rigid segments formed by the reaction of the diisocyanate (e.g., methylene diphenyl diisocyanate – MDI, or toluene diisocyanate – TDI) and the chain extender (e.g., ethylenediamine or 1,4-butanediol). These segments have stronger intermolecular forces (like hydrogen bonding) that provide strength and prevent the fiber from permanently deforming after stretching.
The arrangement and ratio of these soft and hard segments can be tailored during the manufacturing process to achieve specific stretch and recovery properties.
Key Structural Features:
- Segmented Polyurethane Polymer: The alternating soft and hard segments are crucial for spandex’s unique elasticity and strength.
- Soft Segments for Elasticity: The long, flexible chains can extend under stress.
- Hard Segments for Strength and Recovery: The more rigid segments provide anchoring points and help the fiber return to its original shape.
- Cross-linking: Some degree of cross-linking between the polymer chains also contributes to the fiber’s elastic recovery.
In our next lecture, we will explore the remarkable properties of spandex fibers, focusing on their exceptional elasticity, strength, durability, and other characteristics that make them so valuable in the textile industry.
Thank you for your attention.