Regenerated Cellulosic Fiber: Acetate Rayon – A Detailed Lecture (#6 in a Series on Cellulosic Fibers)
Good morning, everyone. Welcome back to our exploration of cellulosic fibers. Following our discussion on viscose rayon, today we delve into another significant regenerated cellulosic fiber: Acetate Rayon. Often grouped with viscose, acetate rayon possesses distinct characteristics and a unique production process that sets it apart.
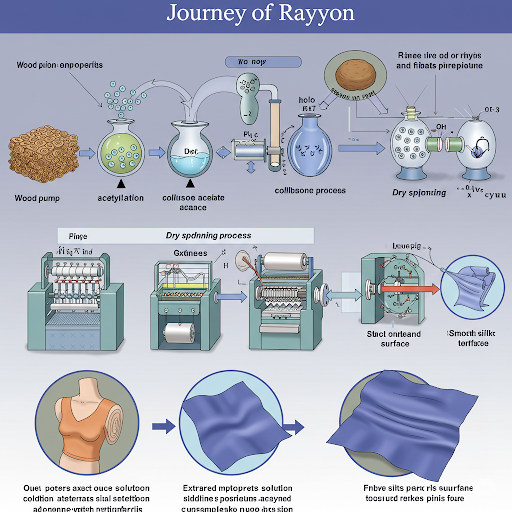
Acetate rayon, like viscose, is derived from natural cellulose sources such as wood pulp or cotton linters. However, instead of completely regenerating the cellulose, the process for acetate involves the esterification of cellulose, specifically the introduction of acetyl groups. This modification results in a fiber with different properties and applications compared to viscose. Acetate was the second manufactured fiber to be produced commercially, after viscose, and it also played a crucial role in the development of the textile industry.
The Production Process of Acetate Rayon:
The production of acetate rayon involves a series of chemical transformations:
- Source Material: Similar to viscose, the starting material is purified cellulose obtained from wood pulp (often from sustainable sources) or cotton linters. This high-quality cellulose is essential for the subsequent reactions.
- Acetylation: The purified cellulose is treated with a mixture of acetic acid and acetic anhydride in the presence of a catalyst, typically sulfuric acid. This process, known as acetylation, replaces some of the hydroxyl (-OH) groups in the cellulose molecule with acetyl (-COCH₃) groups, forming cellulose acetate. The extent of acetylation determines the type of acetate produced:
- Primary Acetate (Cellulose Triacetate): When all or nearly all the hydroxyl groups are acetylated. This form is less common in textiles due to its limited solubility in conventional solvents.
- Secondary Acetate (Cellulose Diacetate): This is the commercially significant form. It is produced by the partial hydrolysis (deacetylation) of cellulose triacetate, removing some of the acetyl groups and making it soluble in acetone.
Cellulose - (OH)₃ + 3 CH₃COOH → Cellulose - (OCOCH₃)₃ + 3 H₂O (Simplified for Triacetate)
For secondary acetate, the reaction is followed by controlled hydrolysis to remove some acetyl groups. - Preparation of Spinning Solution (Dope): The secondary cellulose acetate flakes are dissolved in a volatile solvent, typically acetone, to form a viscous solution known as the “dope.” The concentration and viscosity of the dope are carefully controlled to ensure proper spinning. The use of acetone is a key difference from the viscose process.
- Spinning (Dry Spinning): Acetate rayon is produced using the dry spinning method. The dope is pumped through spinnerets into a spinning cabinet filled with warm air. As the filaments travel down the cabinet, the acetone evaporates, leaving behind solid filaments of acetate rayon. The solvent recovery system is crucial in dry spinning for economic and environmental reasons, as acetone can be recovered and reused.
- Drawing and Stretching: As the filaments emerge from the spinneret, they are often stretched or drawn to align the polymer molecules, which increases the fiber’s strength and uniformity.
- Winding: The solidified acetate filaments are wound onto bobbins or other packages for further processing into yarns and fabrics.
- Optional Treatments: The acetate fibers or yarns may undergo additional treatments such as dyeing, sizing, or finishing to achieve the desired aesthetic and performance characteristics. Acetate requires special dyes, known as disperse dyes, as it does not readily accept dyes used for cellulosic fibers like cotton or viscose.
Characteristics of Acetate Rayon Fiber:
Acetate rayon exhibits a unique set of properties that distinguish it from other cellulosic fibers:
- Structure: Acetate fibers have a lobular or multi-lobed cross-section, which contributes to their characteristic luster and soft hand. Longitudinal striations may also be visible along the fiber length.
- Chemical Composition: It is cellulose acetate, an ester of cellulose. The presence of acetyl groups alters the fiber’s properties compared to pure cellulose.
- Length: Acetate is produced in both filament and staple fiber forms.
- Fineness: The fineness can be controlled during manufacturing.
- Strength (Tenacity): Acetate has low to moderate strength, significantly weaker than cotton, linen, or even viscose rayon, especially when wet. Dry tenacity ranges from 1.1-1.4 gm/denier, and wet tenacity is around 0.6-0.9 gm/denier.
- Elasticity: Acetate has poor elasticity and resilience, leading to wrinkling. It does not readily return to its original shape after stretching.
- Absorbency: Acetate has lower moisture absorbency (around 6.5% moisture regain) compared to other cellulosic fibers like cotton or viscose. This lower absorbency contributes to its faster drying time but also affects dyeability.
- Breathability: While not as breathable as cotton, acetate offers some breathability due to the fabric structure.
- Thermal Properties: Acetate is thermoplastic, meaning it softens and melts when heated. It softens around 205°C and melts around 232°C. This thermoplasticity allows for permanent pleating and shaping but also requires care during ironing.
- Luster: Acetate has a high, attractive luster, often described as silklike, which is one of its key aesthetic appeals. The luster can be modified during production.
- Affinity for Dyes: Acetate requires specific disperse dyes for coloration. It does not dye well with dyes used for cotton or viscose. Cross-dyeing with other fibers in blends is possible due to this difference in dye affinity.
- Resistance to Static Electricity: Acetate tends to have low static cling compared to some synthetic fibers.
- Effect of Chemicals: Acetate is susceptible to hydrolysis by acids, which can break down the polymer. It has fair resistance to weak alkalis but can be damaged by strong alkalis. It is soluble in acetone and other organic solvents like ketones and chloroform.
- Biodegradability: Acetate is derived from cellulose and is considered biodegradable, although the rate of degradation can vary depending on conditions and the degree of acetylation.
- Comfort: Acetate has a soft, smooth hand and good drape, making it comfortable to wear, especially in blends.
- Drape: Acetate fabrics exhibit excellent drape, contributing to elegant and flowing garments.
- Resistance to Mildew and Moths: Acetate is generally resistant to mildew and moth damage.
End Uses of Acetate Rayon Fiber:
The aesthetic and performance properties of acetate rayon make it suitable for a variety of applications:
- Apparel: Acetate is widely used in linings (often as “taffeta lining” in jackets and coats), blouses, dresses, skirts, lingerie, graduation gowns, neckties, scarves, and special occasion wear due to its luster, drape, and soft hand, often as a more affordable alternative to silk.
- Home Textiles: It finds use in draperies, curtains, upholstery, and quilted items due to its appearance and drape. However, its lower abrasion resistance limits its use in high-wear upholstery.
- Industrial Applications: Acetate is used in cigarette filters due to its filtration properties. It also has niche applications in spectacle frames, plastic films, and fiber-tip pens.
- Blends: Acetate is frequently blended with other fibers like silk, wool, cotton, and synthetic fibers (e.g., nylon, polyester) to enhance properties such as wrinkle resistance, strength, or hand.
Environmental Considerations of Acetate Rayon Production:
The production of acetate rayon has environmental implications that need to be considered:
- Source of Cellulose: While derived from renewable resources, the sustainability of wood pulp sourcing is crucial. Utilizing pulp from sustainably managed forests is essential.
- Use of Chemicals: The process involves acetic acid, acetic anhydride, and sulfuric acid. Proper handling, recycling, and waste management are necessary to minimize environmental impact.
- Solvent Recovery: The dry spinning process uses acetone, a volatile organic compound. Efficient solvent recovery systems are vital to reduce emissions and recycle the acetone.
- Water Usage: Water is used in washing and other stages of production, and proper wastewater treatment is necessary.
- Biodegradability: While cellulose acetate is biodegradable, the rate and conditions required for degradation are important factors to consider in its lifecycle assessment.
Efforts are being made to improve the sustainability of acetate production through responsible sourcing of cellulose and closed-loop systems for chemical and solvent recovery. Newer materials like “bio-acetate” are also emerging, often using a higher percentage of plant-based plasticizers.
Conclusion:
Acetate rayon, as the second commercially produced manufactured fiber, offered a lustrous and drapable alternative to natural silk. Its unique production process, involving the acetylation of cellulose and dry spinning, results in a fiber with distinct properties – a soft hand, appealing luster, and good drape, but with lower strength and absorbency compared to other cellulosic fibers. Understanding its characteristics, applications, and environmental considerations provides a comprehensive view of this important fiber in the textile landscape.